What Are Mock-ups? 5 Questions to Ask Your Contractor
The goal of any construction project should always be to build it right the first time. If it is, the building will likely be on schedule, within budget, high quality and one that the end users – whether blackjack dealers or biochemists – are happy with.
That’s why, when choosing a contractor, you’ll want to select a team that uses design and construction mock-ups to keep rework to a minimum. Below we explain what mock-ups are in construction projects and the five most important questions about mock-ups to ask any prospective designer, builder, or engineering, procurement and construction (EPC) firm.
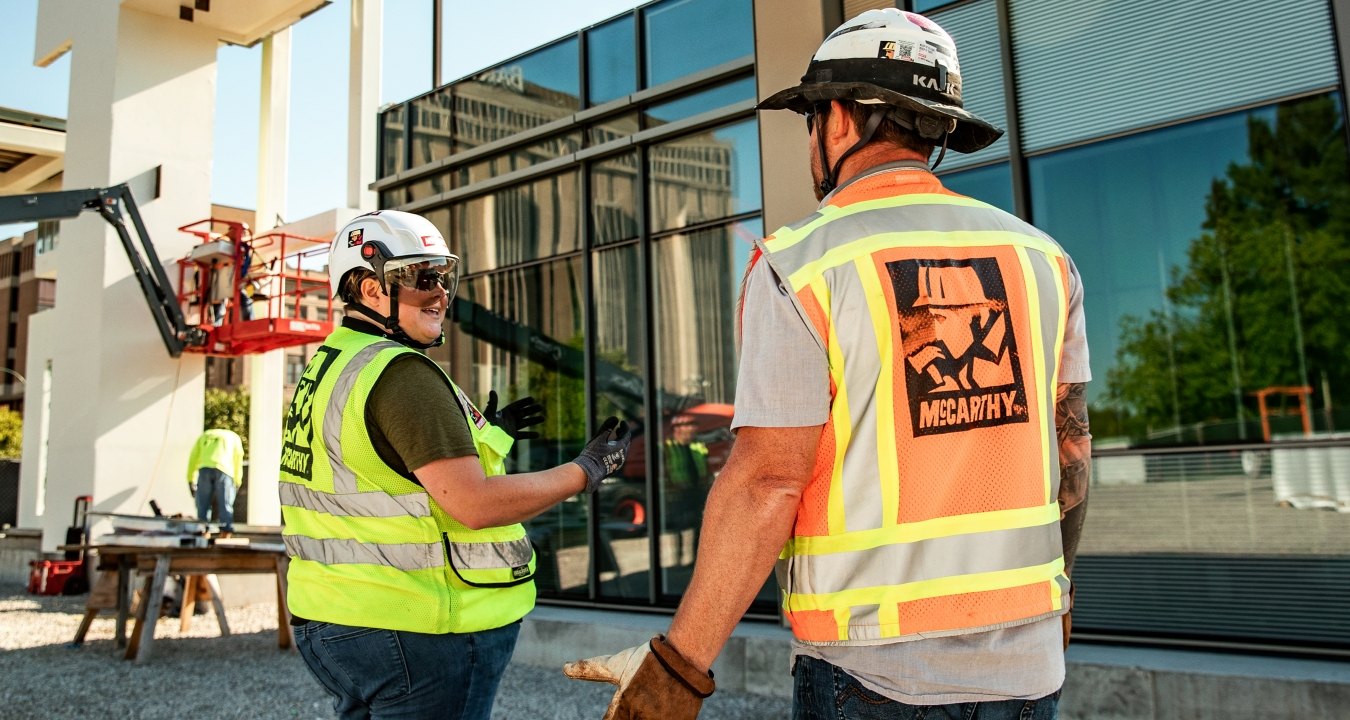
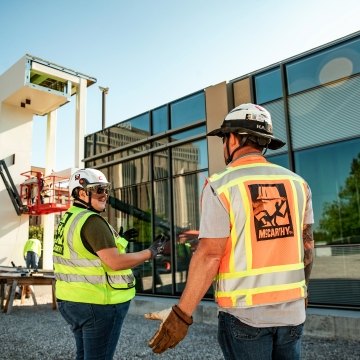
What Is a Mock-up in Construction?
In construction, mock-ups are a representation or full-size model of the proposed work. They’re created to help project teams evaluate design and construction details or test performance before a commitment to further work is made.
Mock-ups can be used for a variety of purposes, including:
- Testing performance, such as static air infiltration, water penetration and structural performance.
- As a reference point for the on-site project team.
- As a visual to show members of the community or investors what will be built.
- To identify constructability issues.
- To optimize installation techniques before actual work begins.
There Are Different Types of Mock-ups
There are three common types of mock-ups that a contractor should have experience with, as they each serve a different purpose.
Stand-alone mock-up
A stand-alone mock-up is a freestanding independent structure that can be used to analyze a specific part of a build. These mock-ups can be created before any significant construction begins (such as during the design phase). They’re commonly used by end-user groups to refine project requirements and resolve issues.
In-place mock-up
In-place mock-ups are mock-ups that are created at full scale and incorporated into the final structure. Common examples include below-grade waterproofing, drywall finish and caulking. In-place mock-ups need to be carefully scheduled to allow for issues to be addressed and resolved before proceeding with production work.
Virtual mock-up
Virtual mock-ups are digital models, often in 3-D, created when early input is desired, when it’s impractical to complete a physical mock-up or as a precursor to a physical mock-up. Virtual mock-ups can be used to identify and evaluate potential building performance issues, while still understanding their limitations.
What to Ask Your Contractor About Mock-ups
Asking these five questions will help you select a vendor who can get the most out of mock-ups to make your project less costly and your end users more satisfied.
1. How will mock-ups be used?
A good contractor should be engaged early with the project owner, end-user groups, architect and key subcontractors to evaluate areas that require mock-ups. This allows the team to address and resolve issues before any significant impact on cost or schedule occurs. In addition to identifying areas that require mock-ups, the contractor should tell you who will be constructing the mock-ups. It’s important to have the same crews who create the mock-ups do the actual build. A subcontractor utilizing their top performers to do the mock-up but assigning others to complete the process in the field will not create repeatable results.
2. Which mock-ups are right for the project?
Not everything requires a mock-up. But costly or often repeated aspects of your build (e.g., mechanical systems, lab casework, patient headwalls, bathrooms, interior finishes, exterior skin details and window penetrations) should be considered for mock-ups. Be sure to have a clear understanding of the purpose of each mock-up, as they can be costly. For instance, exterior mock-ups may be necessary to analyze how constructed details hold up to the weather and interior mock-ups may be used to explore the relationship of different finishes or transitions between materials.
3. How will user groups be engaged?
Key stakeholders should be engaged early in determining necessary mock-ups to ensure all user-group needs are represented and to avoid costly changes later. User groups included in this early collaboration should be the project owner, designer, contractor, subcontractors and consultants. Together, these groups should agree on and document what’s considered acceptable quality in a mock-up and the process for achieving this. Designs and mock-ups should be reviewed by key user groups for feedback.
4. What’s considered acceptable quality on a project? How will quality goals be met?
Quality should be embedded in your contractor’s process and culture, not tacked on as an afterthought. Your team should discuss the potential use of mock-ups to help achieve quality early in the planning process. A contractor with a thorough and formalized approach to mock-ups should be able to outline their approach to documenting each of the following steps:
- Planning the mock-up
- Completing the mock-up
- Testing the mock-up
- Resolving issues
- Repeating the steps in the field
Mock-up results must be documented to enable better planning and sequencing of construction.
5. What steps are taken to prevent the building from leaking?
Potential water infiltration is one of the most significant concerns voiced by owners. It’s critical to make sure your contractor has a formalized approach to plan for testing and evaluating a building’s enclosure performance. Ask about their approach and make sure they utilize a third-party reviewer throughout their process and complete building enclosure performance mock-ups.
Utilize Mock-ups for a Quality Build
Mock-ups provide the opportunity to positively impact the final cost, the schedule and the quality of the finished product. Ask your potential builders the five questions above, and you’ll feel comfortable knowing you have the right player on your team. Learn more about working with McCarthy and our collaborative processes when you contact us today.