Georgia Tech Engineered Biosystems Building
Atlanta, GA
Project Stats
Client
Georgia Institute of Technology
Project Status
Complete
Markets
The Engineered Biosystems Building serves as the focus for Georgia Tech's efforts to improve human health through an enhanced understanding of complex living systems. The building co-locates and integrates faculty and students from the Colleges of Sciences, Engineering and Computing.
ZERO
Lost Time Accident Rate
218,800
Square Feet
The Challenge
The project’s fast-track nature required ingenuity and teamwork from the project’s outset. McCarthy was contracted to serve as construction manager-at-risk only a few weeks after design was awarded. At this time, the EBB was just an idea and no conceptual drawings existed. Extensive collaboration was immediately required among Georgia Tech, the design team and McCarthy to align goals, eliminate risks and ensure the project’s success.
Geotechnical conditions at the site generated the project’s greatest challenges. Situated at the historic headwaters of the Atlanta water system, the foundation design was elevated by three feet to accommodate a high water table. The team also performed a number of tests to assess the situation, and prepared for potential groundwater infiltration. This advanced planning paid off when extensive spring rains brought an underground riverbed back to life, submerging the entire west side of the site during excavation. In response, construction crews installed a temporary dewatering system of roughly 20 deep wells, each fitted with a pump connected to a main header line running along the inside of the shoring wall. The rains and riverbed produced so much water that the system was pumping up to 600 gallons per minute.
Laboratories are commonly known for their high energy use due to the intense mechanical and electrical demands needed to power the equipment inside. Focused on making this project as sustainable as possible, the project team was committed to incorporating and tracking leading technologies for efficient water and energy use, meeting the university’s goal for LEED Platinum building certification.
Working within limited space in a high-traffic downtown area imposed another hurdle. The team adapted by implementing an extensive communication, safety and logistics plan, including alternating construction entrances and widening a street that later provided access to the loading dock. An abundance of signage was also created to keep students, faculty, and visitors safe, and a project-specific social media campaign was launched to engage the community, as well as to provide construction updates and traffic information throughout the project.
Ultimately we are all working to fight disease and save lives. EBB is designed to foster the research to do just that.
Georgia Tech Professor and Chair of the School
The How
In order to meet the fast-track schedule, the project was broken down into four packages. This phasing strategy enabled construction to commence eight months after design began, and played an important role in the project’s on-time completion. With funding for the university’s research hinged on the building’s opening date, there was little room for extending the project schedule.
Ensuring the budget for this cutting-edge research facility required additional expertise and innovation. Working with the design team, McCarthy presented more than 200 value-management alternates across all engineering disciplines, allowing Georgia Tech the greatest amount of options with the least impact to overall function, quality and design intent.
Target Value Design, a lean process, was also used to ensure the project’s budget throughout preconstruction and construction phases, ultimately maximizing the program and providing the best final cost for Georgia Tech.
Although the emergence of the buried riverbed during excavation complicated construction, the team turned this precious water resource into a sustainable design asset by incorporating a unique water-harvesting component. To permanently extract the groundwater, the EBB foundation was fitted with a dewatering system that pumps the groundwater to a 10,000-gallon cistern on the northwest corner of the building. This water is primarily harvested for gray water use, with overflow feeding a water feature and a wetland pond on the site.
A second 14,200-gallon cistern on the building’s northeast corner collects run-off from the wetlands, the building’s east-side roof drains and the north-elevation storm drains. The water is then pumped to a cistern at the nanotechnology building, where it is used for campus-wide irrigation.
During the design and planning stages, energy modeling was performed to calculate the building envelope with precision accuracy. As a result of these studies, the laboratories feature high-efficiency fume hoods, automatic sash closers and energy-efficient lighting control systems to conserve energy. Additional energy efficient features include photovoltaic panels, exterior sunshades, expansive low-e glazing in lab and circulation areas, and 365 chilled beams strategically positioned in labs, service corridors and other areas where excess heat may be generated. Requiring chilled water piping for the beams, as well as conventional ductwork, further congested the labs' crowded overhead areas. To eliminate conflicts and coordinate this area, the team used Building Information Modeling (BIM) before construction began.
As a quality control measure, field mock-ups of the laboratory spaces, graduate student areas, monumental stairs, exterior skin, and various other complex areas were constructed. The exterior skin mock-up delivered the most value, revealing important opportunities for improvement in areas such as the sunscreens and window screens. Performing these changes during the mock-up process was significantly less expensive than changing them during construction. It also allowed the team to test the integrity of the exterior system for air and water infiltration, making it a critical component of the quality plan.
The building symbolizes what Georgia Tech is all about — collaboration and innovation.
Georgia Tech President
The Outcome
Much like the interdisciplinary scientific achievements research teams will produce inside Georgia Tech’s Engineered Biosystems Building, the project’s collaborative design and construction process will serve as a model for other academic institutions to emulate. Bringing together the design and construction team early in the process helped the team manage risks, implement innovations and determine the best choices to mitigate the many challenges on this innovative academic research facility project.
The facility also served as a live laboratory long before it opened. During construction, several teams of engineering students and researchers took advantage of the construction site to conduct experiments. One group analyzed productivity and safety by using both GPS and unmanned aerial vehicles to track equipment and personnel, while another team used augmented reality to check product installations via hand-held tablets in the field to compare them with BIM digital planning models. Student groups also studied the use of BIM for masonry productivity and preformed air quality testing to ensure conditions were always in safe limits.
Now that Georgia Tech’s revolutionary facility is complete, researchers from various scientific disciplines will have the holistic space required for discovering new biomedical breakthroughs to combat life-threatening conditions like cancer, heart disease and diabetes. Putting Georgia Tech at the forefront of biosciences and bioengineering research, the EBB is also positioned to generate substantial economic impacts in the region through new grant opportunities, the creation of high-skilled, well-paying jobs, and the commercialization of newly developed technologies or research findings.
This is a complicated building… We were able to bring the project in on budget, in part because we did a good job of risk management and were able to work on a prioritized basis.
Georgia Tech Director of Design and Construction
Awards and Recognition
LEED Platinum Certified

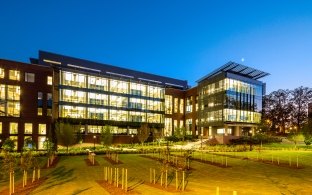
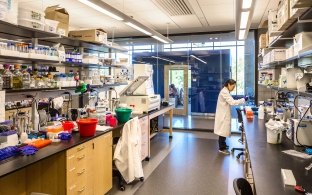
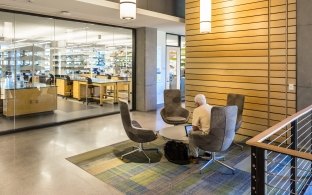
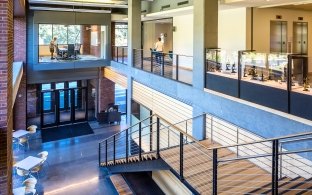

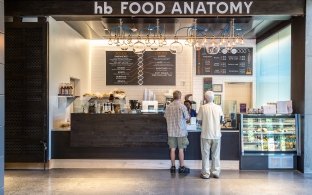
Consultant
Research Facilities Design
Architects
Cooper Carry, Inc.
Lake | Flato Architects
Trade Partner
Mann Mechanical
Engineers
Newcomb & Boyd
Uzun & Case Engineers
Long Engineering