Ocotillo Water Reclamation Facility
Chandler, AZ
McCarthy and Sundt Construction Inc., were the joint venture general contractor for the Ocotillo Water Reclamation Facility (OWRF) expansion and process Improvement projects for the city of Chandler, Ariz.. The project, named ENR Southwest Best Project of the Year (Water/Environment), included new construction and upgrades to the existing plant.
The OWRF expansion project included upgrades to the existing 10-mgd wastewater treatment plant and the construction of an expansion facility that was built for a future capacity of 30-mgd. The new facility utilizes membrane bioreactor technology (MBR), the combination of activated sludge treatment together with a separation of the biological sludge by micro- or ultra-filtration membranes. The technology allows for a smaller footprint and reduced sludge production.
For years, the 10-mgd OWRF plant has been considered an innovator because it recycles all its treated water. The water is placed in storage lakes, recharged to the aquifer, sent to an industrial user or sent to an adjacent Native American community for agricultural use.
The design and construction were done with the intention of allowing for ease and lower cost efficiency for future capacity and expansion.
Innovative weekly updated drone videos were used during weekly progress meetings to help visualize construction progress. This gave the team an opportunity to coordinate discussions and decision making quickly by having the drone video information right there on a 65-inch screen at the meeting.
The team developed a community outreach plan that included development of a Community Advisory Panel (CAP) consisting of key stakeholders from the nearby commercial, industrial and residential neighbors. We facilitated several informational meetings with the CAP early in the conceptual design phase, educating them on the need for the city to increase its treatment and reuse capacity closer to its end users by expanding the OWRF.
The Challenge
During preconstruction, we identified the needs and wants of the project were potentially exceeding the project’s budget prior to the start of construction. As a Construction Management At-Risk (CMAR) partner in the preconstruction efforts, Sundt/McCarthy was able to contribute accurate estimating services that allowed the owner and designer to make budget-aware decisions to keep the project on schedule.
The team was able to avoid common industry schedule and quality pitfalls by aggressively avoiding procurement delays; questioning design imperfections early and using past self-perform experience to efficiently sequence and install complex wastewater systems. This would not have been a success without the experience and knowledge of employees from past water and wastewater projects.
As a joint venture project, both management staff and the self-perform craft teams from Sundt Construction and McCarthy were able to combine the individual company cultures and standard working practices together in order to perform the work in a safe, productive and quality driven manner. This combined effort was planned out in the field with the superintendents by applying the necessary best practices of both companies in executing challenging work in each of the major self-perform disciplines.
If the combined companies’ craft felt more inclined to utilize the practice of one company over the other for strategic safety or production reasons in specific applications, it was implemented. This was a common practice throughout the lifecycle of the project, where different concrete structures and different piping systems had different challenges that allowed the ability of the JV team to implement the best applied construction strategies of both JV companies.
During the Phase 1 OWRF Expansion, the team faced many challenges including maintaining operations of the existing OWRF during the construction activities. There were over 30 scheduled shutdown events where construction activities impacted plant operations. Through the use of effective coordination meetings between City Operations staff, Carollo Engineers, and Sundt-McCarthy, the plant maintained permit discharge requirements at all time of construction.
The Outcome
As a Joint Venture, Sundt/McCarthy maximized quality and craftsmanship by pulling craft resources from two nationally recognized treatment plant builders. The ability to acquire quality tradespeople from both companies gave the project the best of the best, ensuring top-quality results on the project. This further allowed the JV to provide added resources to focus on multiple areas of the project at once to complete the project in an efficient manner.
Recognizing the need to replenish and further develop a declining construction craft labor force, Sundt embraced and invested in the National Center for Construction Education and Research. This effort proved beneficial throughout the project to ensure the development of a safe, productive and sustainable workforce through training, assessment, certification and career development of craft professional. As a result, the project experienced notably fewer quality deficiencies and less rework.
The OWRF expansion has been programmed to allow for an ultimate buildout capacity of 30 MGD, on land adjacent to the existing OWRF to the north and west, over several phases. The preliminary design development stage focused on planning the site through the phases to the 40 MGD buildout (new 30 MGD trains plus existing 10 MGD train). This planning included provisions to allow ease of future expansions, such as diversion structures, piping corridors, electrical ductbank corridors, footprints for all treatment facilities, and piping to maintain minimum and maximum flow rates through all phases, to ultimately avoid costly plant shutdowns or bypassing.
Considerable attention and funds were allocated to being a good neighbor. All process basins were covered and all foul air was directed to two-stage biological odor control treatment systems, followed by carbon adsorption for polishing. Attention was also paid to noise mitigation. Equipment was specified to meet specific maximum decibel limits, and all nose-generation equipment (pumps, blowers, etc.) were en enclosed within buildings or located below-grade.
The project team was interested in providing aesthetically pleasing views of this new wastewater treatment plant for nearby multi-story business buildings (their neighbors). The owner and design engineer worked to provide canopies, structural tilts and architectural features not common or required for the industrial environment of a Wastewater treatment plant.
Efforts were also made to distance the feel of an industrial wastewater plant from the adjacent major streets and intersections by including berms and aesthetically pleasing landscaping between the new facility and the public.
To save capital costs while increasing treatment capacity, the project team employed innovative approaches, including the construction of combined facilities that could serve both the existing conventional and the new MBR treatment trains. The conventional and MBR treatment trains now utilize shared Headworks, Solids Handling, and Reclaimed Water Pumping facilities to replace older, less efficient systems.
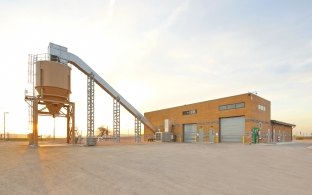
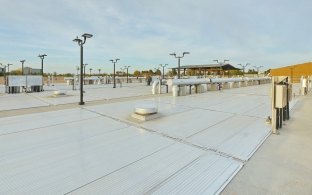
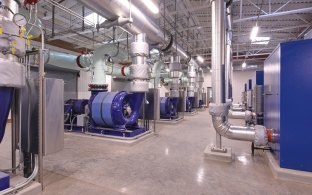
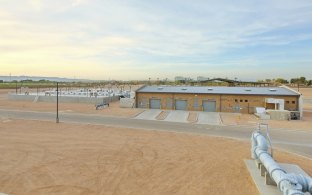
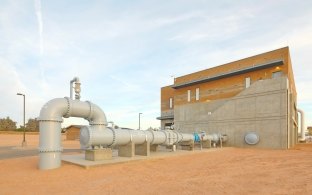
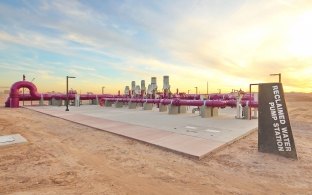
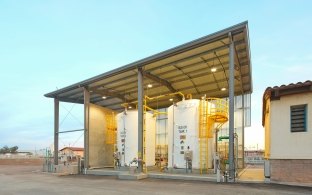
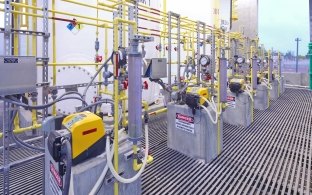
Joint Venture Partner
Sundt Companies
Engineers
Carollo Engineers
Wilson Engineers